Inventory Control
Overview of Inventory Control
Definition of
Inventory Control

What is Inventory Control? Inventory Control, also known as stock control, is the process of ensuring that appropriate amounts of inventory are maintained by a business to meet customer demand without incurring excessive holding costs or stockout situations. It involves supervising the supply, storage, distribution, and recording of inventory. Effective inventory control aims to optimize inventory levels, minimize investment in inventory, and ensure that items are available when and where they are needed. It is a critical component of broader inventory management.
Activities Related to
Inventory Control

Here is a list of Inventory Control related activities:Â
Setting reorder points and safety stock levels, Implementing stocktaking or cycle counting procedures, Utilizing an inventory control system (manual or computerized) for tracking, Analyzing inventory turnover rates and Days Sales of Inventory (DSI), Managing stock locations and warehouse organization, Identifying and dealing with obsolete or slow-moving inventory, Applying methods like ABC analysis to prioritize control efforts, and coordinating with suppliers for timely deliveries as seen in Just-in-Time (JIT) systems.
These activities help businesses maintain optimal stock levels and manage associated costs.
The Importance of
Inventory Control
Effective Inventory Control is crucial for businesses as it directly impacts operational efficiency, customer satisfaction, and financial health. Good control prevents overstocking, which ties up working capital and increases risks of obsolescence and storage costs. It also avoids understocking, which can lead to lost sales, production delays, and dissatisfied customers. By optimizing inventory levels, businesses can reduce costs, improve cash flow, and enhance profitability. Furthermore, strong inventory control provides accurate data for financial reporting (e.g., valuing inventory on the Balance Sheet and calculating COGS) and strategic decision-making, such as determining the Economic Order Quantity (EOQ).
Key Aspects of
Inventory Control

Stock Optimization
Balancing the need to have enough inventory to meet demand with the desire to minimize holding costs.
Cost Reduction
Aims to reduce costs associated with ordering, storing, and managing inventory, as well as losses from obsolescence or damage.
Tracking and Monitoring
Involves continuous tracking of inventory levels, movements, and values, often through an inventory control system.
Process Improvement
Focuses on improving the processes related to ordering, receiving, storing, and issuing inventory to enhance efficiency and accuracy.
Concepts Related to
Inventory Control
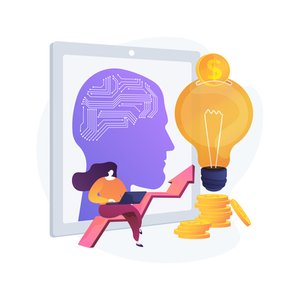
Inventory Control is a key function within Inventory Management and the broader Supply Chain Management. It utilizes tools and techniques like setting reorder points, safety stock levels, and methods such as Economic Order Quantity (EOQ) and Just-in-Time (JIT). Accurate inventory valuation methods are also crucial for effective control.
Inventory Control
in Action:
The Adventures of Coco and Cami
Coco and Cami are learning how to keep just the right amount of supplies on hand. Professor A explains Inventory Control and how it helps them avoid running out of ingredients or having too much stock spoil.
Discover with Coco and Cami the techniques they can use, like setting reorder points, to manage their inventory effectively and keep their businesses running smoothly.
Take the Next Step
Effective Inventory Control can save your business money and improve customer satisfaction. If you need assistance implementing inventory control methods or systems, schedule a free 30-minute consultation.
Contact Sales for a Free Consultation