Just-in-Time (JIT)
Overview of Just-in-Time (JIT)
Definition of
Just-in-Time (JIT)

What is Just-in-Time (JIT)? Just-in-Time (JIT) is an inventory management and production strategy where materials, components, and products are ordered and received from suppliers only as they are needed in the production process or to meet customer demand. The primary goal of JIT is to minimize inventory holding costs, reduce waste (including storage space, spoilage, and obsolescence), and improve overall operational efficiency. It's a core component of lean manufacturing principles, aiming to streamline production and enhance responsiveness.
Activities Related to
Just-in-Time (JIT) Implementation

Here is a list of JIT related activities:Â
Developing strong relationships and communication channels with reliable suppliers, Implementing precise demand forecasting systems, Designing efficient production scheduling that matches output to demand, Reducing setup times for machinery and processes, Arranging for frequent, small-batch deliveries of materials, Improving quality control processes to minimize defects (as there's no buffer stock), and Continuous process improvement to eliminate waste and inefficiencies in the supply chain.
Successful JIT implementation requires a highly coordinated and efficient operational environment.
The Importance of
Just-in-Time (JIT)
Just-in-Time (JIT) inventory management is important because it can lead to significant cost savings and efficiency gains for businesses. By minimizing inventory levels, companies can reduce warehousing costs, insurance expenses, and losses due to spoilage or obsolescence. This frees up working capital that can be invested elsewhere in the business. JIT also encourages a focus on quality, as defects cannot be hidden by large buffer stocks and must be addressed immediately. Furthermore, it can lead to shorter production cycles and increased flexibility to respond to changes in customer demand. However, JIT systems are also vulnerable to disruptions in the supply chain or unexpected surges in demand, as there is little to no safety stock.
Key Aspects of
Just-in-Time (JIT)

Minimal Inventory Levels
A core principle is to hold the least amount of inventory possible at all stages of production and distribution.
Pull System
Production is often driven by actual customer orders ("pull") rather than by forecasts ("push"), meaning items are made only when needed.
Supplier Reliability
Relies heavily on dependable suppliers who can deliver high-quality materials precisely when needed.
Waste Reduction (Muda)
Focuses on eliminating all forms of waste in the production process, including overproduction, waiting time, excess inventory, and defects.
Concepts Related to
Just-in-Time (JIT)
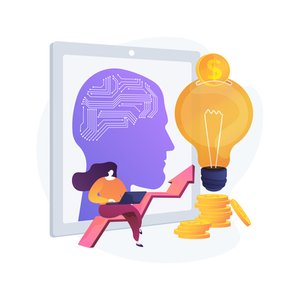
Just-in-Time (JIT) is a key strategy within Inventory Management and is closely associated with lean manufacturing principles. It contrasts with traditional systems that might use Economic Order Quantity (EOQ) to determine larger batch order sizes. Effective JIT requires excellent inventory control and robust supply chain management. While it aims to minimize inventory, its impact on Cost of Goods Sold (COGS) and inventory valuation still needs to be accounted for using methods like FIFO.
Just-in-Time (JIT)
in Action:
The Adventures of Coco and Cami
Coco wants her sandwich bread delivered fresh every morning, just enough for the day. Professor A explains how this "Just-in-Time" approach to inventory can save space and reduce waste.
Learn with Coco and Cami about the benefits of JIT, like lower storage costs, but also the importance of reliable suppliers to make it work for their shops.
Take the Next Step
Implementing a Just-in-Time inventory system can streamline your operations and reduce costs. Curious if JIT is right for your business? Schedule a free 30-minute consultation.
Contact Sales for a Free Consultation