Inventory Management
Overview of Inventory Management
Definition of
Inventory Management

What is Inventory Management? Inventory Management is a systematic approach to sourcing, storing, and selling inventory—both raw materials components and finished goods. It encompasses the entire process from purchasing stock to its final sale, aiming to have the right products in the right place at the right time, and in the right quantity. Effective inventory management balances the costs of holding inventory (storage, insurance, obsolescence) against the costs of not having enough inventory (stockouts, lost sales). It's a crucial aspect of supply chain management and overall business operations.
Activities Related to
Inventory Management

Here is a list of Inventory Management related activities:Â
Demand forecasting, Setting inventory levels (min/max stock, reorder points), Selecting and implementing inventory control systems, Choosing inventory valuation methods (e.g., FIFO, LIFO), Managing supplier relationships and lead times, Implementing inventory optimization techniques like Economic Order Quantity (EOQ) or Just-in-Time (JIT), Conducting regular stock audits and cycle counts, and Analyzing inventory performance metrics such as Days Sales of Inventory (DSI) and turnover rates.
These strategic activities ensure that inventory supports the company's financial and operational goals.
The Importance of
Inventory Management
Inventory Management is incredibly important for businesses because it directly affects customer satisfaction, operational efficiency, and financial performance. Good inventory management ensures that products are available to meet customer demand, preventing lost sales and maintaining customer loyalty. It helps minimize the costs associated with holding too much inventory, such as storage, insurance, and the risk of spoilage or obsolescence. By optimizing inventory levels, businesses can free up cash flow, reduce waste, and improve their bottom line. It's also essential for accurate financial planning and reporting, especially concerning assets on the Balance Sheet and the Cost of Goods Sold.
Key Aspects of
Inventory Management

Demand Forecasting
Accurately predicting future customer demand to guide purchasing and production decisions.
Inventory Cost Control
Managing and minimizing the various costs associated with inventory, including ordering, holding, and shortage costs.
Stock Optimization
Maintaining appropriate levels of all types of inventory (raw materials, work-in-process, finished goods) to balance service levels with cost efficiency.
Process Efficiency
Streamlining the processes involved in ordering, receiving, storing, and distributing inventory. This often involves leveraging an inventory control system.
Concepts Related to
Inventory Management
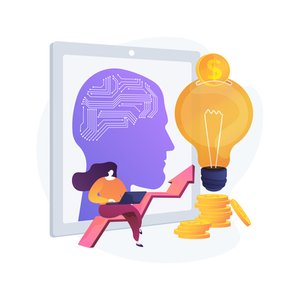
Inventory Management is a broad field that incorporates specific techniques like Inventory Control, Economic Order Quantity (EOQ), Just-in-Time (JIT) systems, and Inventory Valuation Methods such as FIFO and LIFO. It is integral to Supply Chain Management and has a significant impact on a company's financial statements.
Inventory Management
in Action:
The Adventures of Coco and Cami
Coco and Cami are juggling suppliers, storage, and customer orders. Professor A steps in to explain the wider scope of Inventory Management and how it helps them run their businesses smoothly.
Learn with our entrepreneurs about the strategies and systems involved in effective inventory management, from forecasting demand to choosing the right control techniques.
Take the Next Step
Effective Inventory Management is key to optimizing costs and satisfying customers. If you need help developing inventory strategies or systems, schedule a free 30-minute consultation.
Contact Sales for a Free Consultation